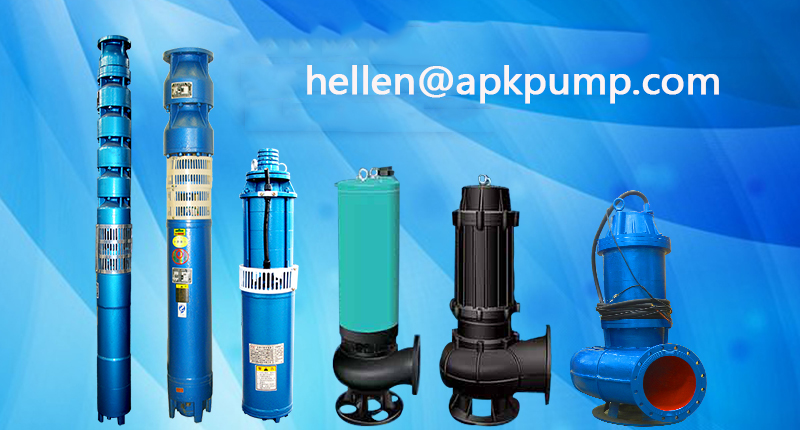
Each product in after a period of time, there will be failures, for after a period of time there may be a decrease in operating efficiency, resulting in decreased efficiency of the pump what are the reasons, take a look:
1. Due to the erosion of water flow, pump channel wall and impeller over the surface becomes rough, the friction coefficient of the flow passage of the pump increases, coupled with water in the pump flow rate is large, head loss increased. Reduction of hydraulic efficiency.
2. Due to the reasons in the pump before adding drugs or water, the serious fouling or corrosion of the pump shell. The pump shell inner severe scaling can make the pump shell wall thickness increased about 2ram, and the water pump scale formed on the inner wall of the pump body tumor volume, reduce the amount of pumping, and channel roughness, head loss increase. Both customer efficiency and hydraulic efficiency decreased.
3. Because the diaphragm pump diaphragm pump casting process caused by defects, cavitation, abrasion, making corrosion and chemical etching and other reasons caused by voids or cracks in the pump flow, water flow vortex caused by the energy loss. Reduction of hydraulic efficiency.
4. The surface of the impeller cavitation. When the back surface of the blade runs negative pressure, when the pressure is Pk<pva, the steam hole and the honeycomb surface are generated.
5. Volume loss and mechanical loss. Because the pump used for a long time, produce leakage and mechanical wear resistance increases, the volume efficiency and mechanical efficiency.
Pump in operation should be observed regularly, so as to be able to detect these faults as soon as possible, timely processing. Early treatment will not cause too much damage to the company.